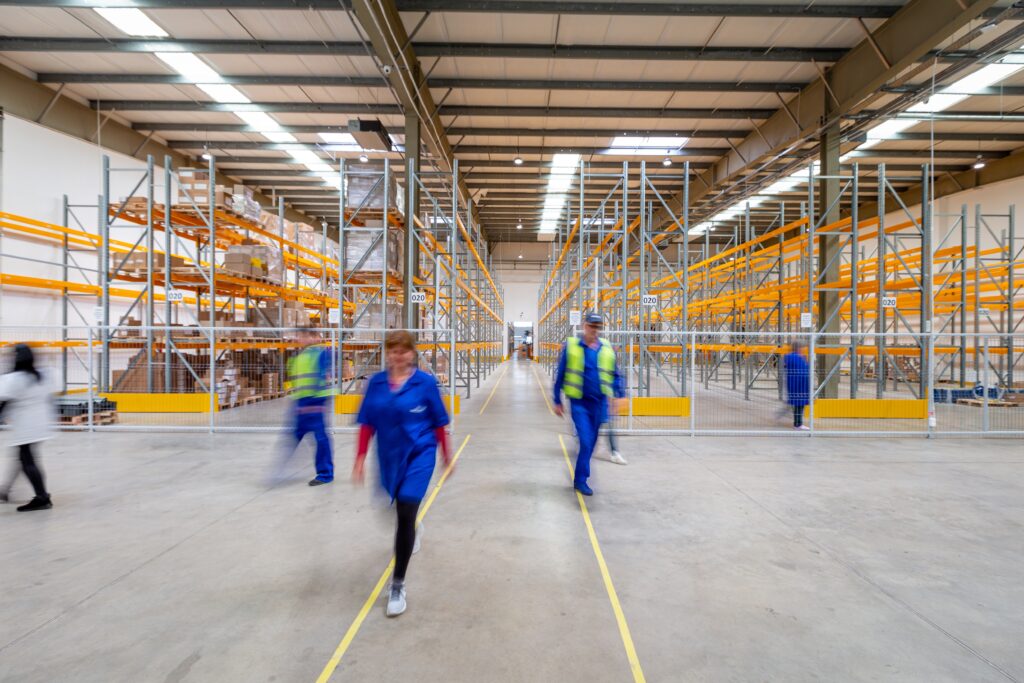
One of the unique challenges warehouse facilities managers face is lighting. Unlike other types of commercial spaces, warehouses, in general, have elevated shelves, wide and open floor spaces, high ceilings, and few windows. All these factors can make it difficult to achieve proper lighting.
It is essential for warehouse lighting to be bright enough so employees can see clearly throughout the space and work efficiently and safely. If a warehouse has poor lighting, they are at greater risk of having a serious accident or making a costly error.
To maintain a productive environment, warehouse spaces require a lighting system that works well so everyone can see properly and perform their tasks better. At the same time, it should also be energy-efficient to help reduce operating costs.
This article enumerates the 5 most important warehouse lighting requirements to ensure safety, increase productivity, and achieve cost efficiency.
5 Warehouse Lighting Requirements for Safety, Productivity, and Cost Efficiency
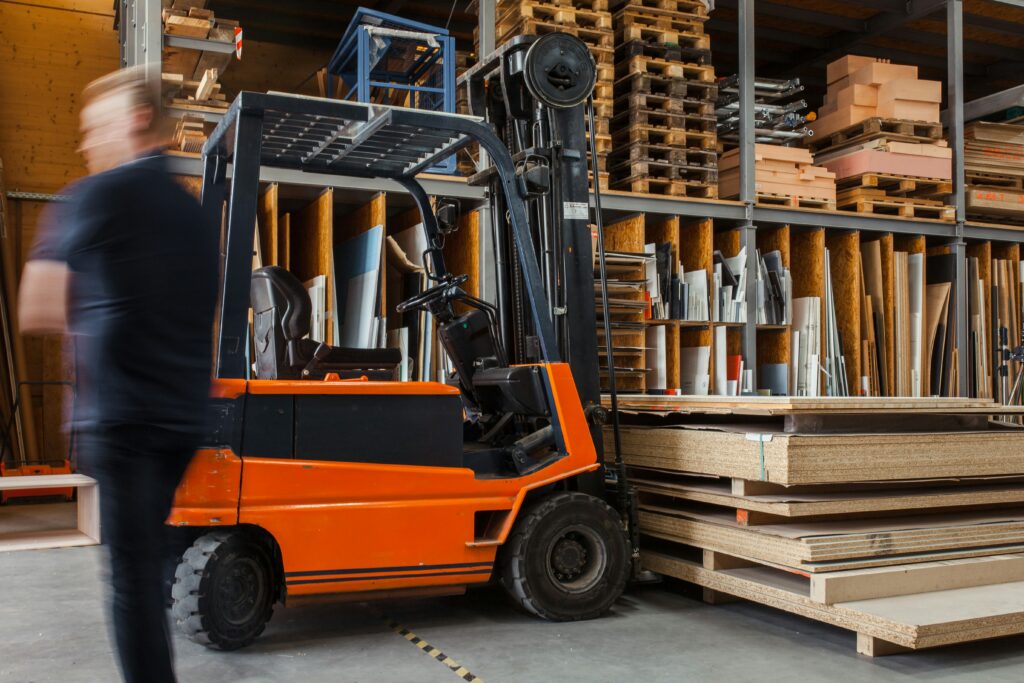
#1: Adequate Illumination Levels
Sufficient lighting is crucial in ensuring safety in the workplace. Proper lighting not only protects your workers from eye strain but also helps to prevent accidents from happening.
The Occupational Safety and Health Administration (OSHA) requires a minimum of 5 foot-candles for warehouses. In its lighting standards, OSHA directs that the amount of light in the workplace should allow personnel to see clearly, as inadequate illumination can cause stress, fatigue, headaches, eye strain, and possibly accidents. Conversely, too much light may lead to glare-induced headaches and stress.
Foot-candle is OSHA’s preferred unit of measurement. A foot-candle refers to the illuminance of one square-foot surface from a uniform source of light. You may refer to Title 29 of the Code of Federal Regulations, section 1926.56, for candle-feet of light required for various types of work.
The Illuminating Engineering Society (IES) recommends the following foot-candle levels to ensure adequate illumination for warehouses and storage facilities:
Facility Type | Average Maintained Foot-Candles (Horizontal) | Range of Maintained Foot-Candles (Horizontal) | Average Maintained Foot-Candles (Vertical) | Range of Maintained Foot-Candles (Vertical) |
Bulky Items – Large Labels | 10 | 5 | ||
Small Items – Small Labels | 30 | 15 | ||
Cold Storage | 20 | 10-30 | 10 | 5-15 |
Open Warehouse | 20 | 10-30 | ||
Warehouse with Aisles | 20 | 10-30 | 10 | 5-15 |
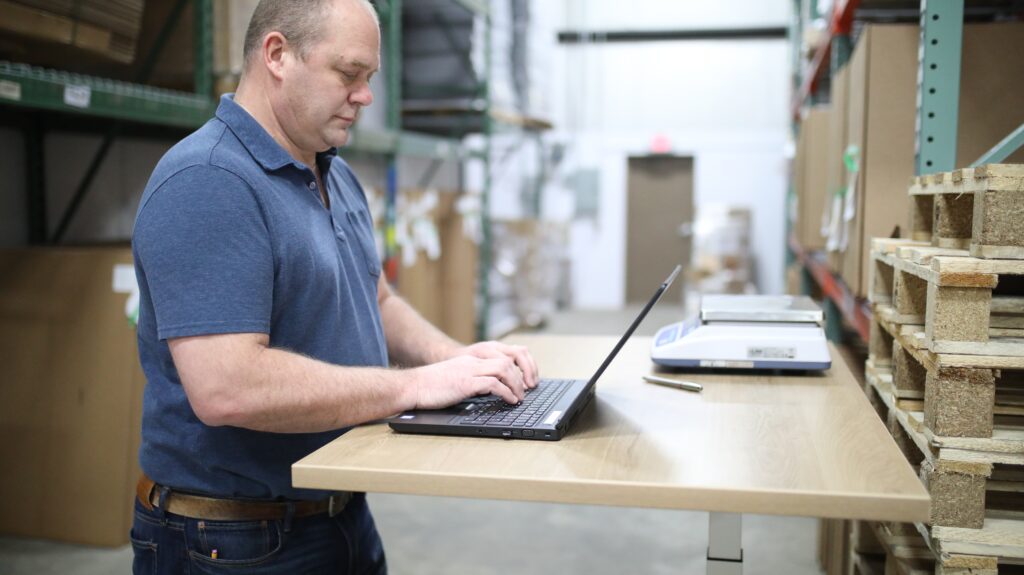
#2: Uniform Distribution of Light
One of the main goals of a warehouse manager is to install high-quality, reliable lighting systems. In a fast-paced warehouse bustling with activity, having the appropriate lighting system facilitates seamless operations and enhances workplace safety.
Generalized lighting in the warehouse should be evenly distributed, without gaps, so that employees can comfortably see and move throughout the workplace without straining their eyes. This helps improve employee performance, increasing their concentration levels and resulting in a productive work environment.
To achieve uniform distribution of light, the illumination pattern in your warehouse must align with your facility’s layout. For example, if an area has narrow aisles and tall shelves, the light source needs to follow a similar long, narrow pattern. Wide open spaces will require a wide illumination pattern.
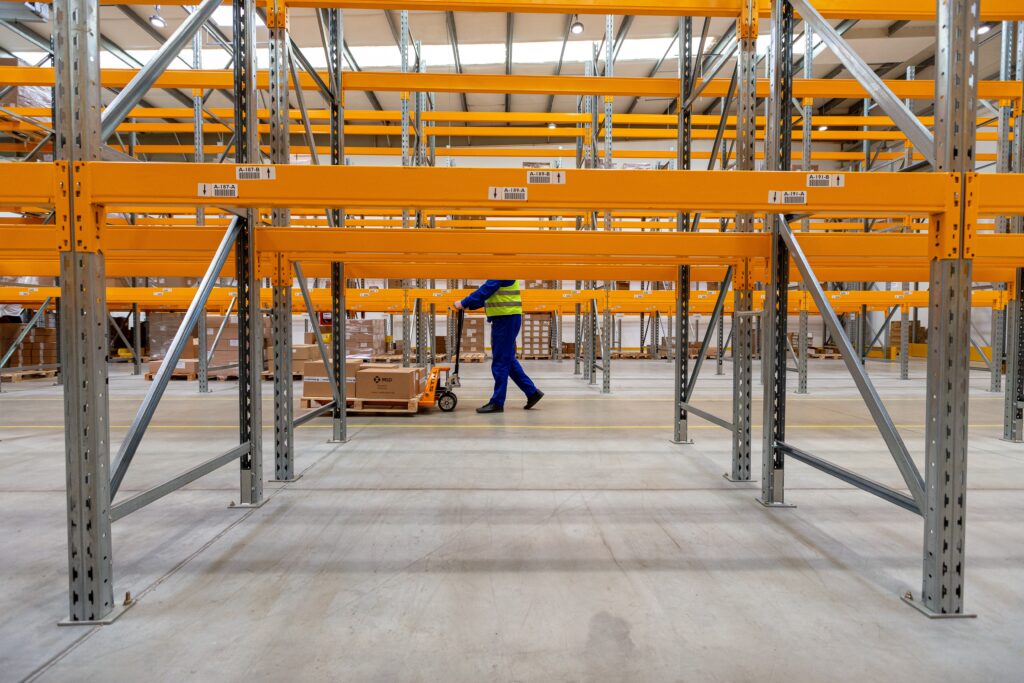
#3: Minimize Glares and Shadows
Having appropriate lighting in the warehouse helps minimize glares and shadows that may cause eye fatigue, headaches, and workplace injuries and incidents. Light fixture spacing plays a major role in creating these glares or dark spots.
When lights are placed too far apart, dark spots are formed, making it difficult to see items clearly with the naked eye. On the other hand, placing light fixtures too close together results in hot spots where the light overlaps. Aside from causing eye strain from the glares, these bright areas can make other parts of the facility look dark. It also contributes to higher overhead costs.
At Forthright LED Lighting, we make it possible for facilities to have a well-lit environment that allows employees to have a positive work experience by creating a lighting design that balances out the illumination all throughout the space. We use a thermal image to show clients how our design ensures even distribution of illumination, eliminating hot spots in their facilities.
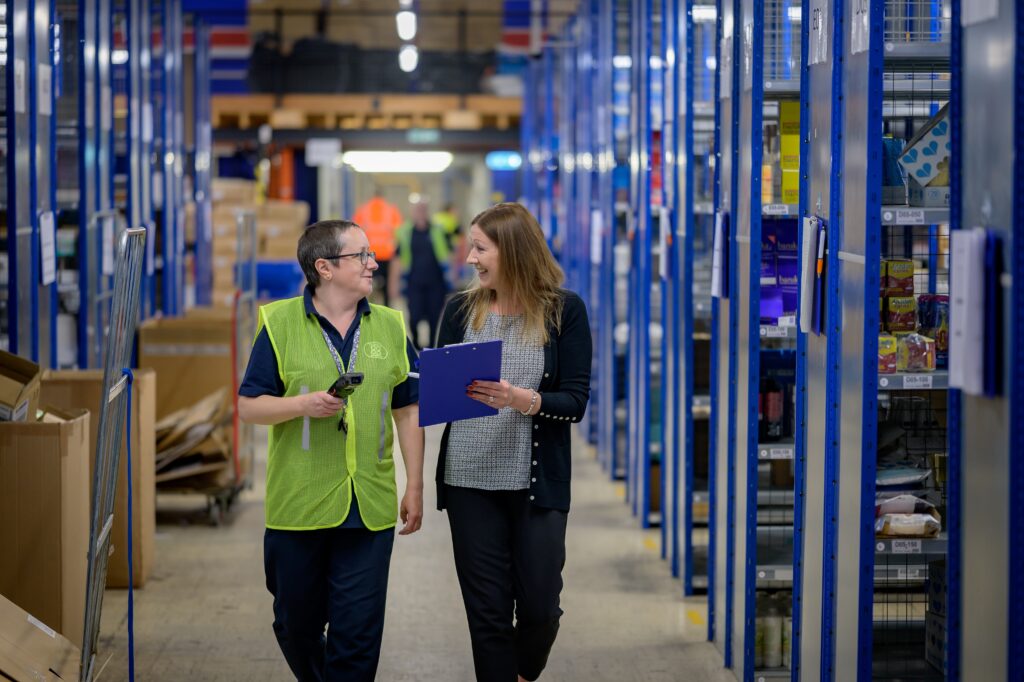
#4: Adherence to Safety Standards and Regulations
Adhering to warehouse lighting requirements and complying with industry and government safety standards is essential for legal and operational reasons.
As of January 2023, OSHA’s maximum penalties for serious and other-than-serious violations have increased from $14,502 per violation to $15,625 per violation. The maximum penalty for willful or repeated violations increased from $145,027 per violation to $156,259 per violation.
However, these penalties are just a small portion of the potential costs of unsafe lighting in the workplace. Insufficient lighting may affect the health, productivity, and safety of your employees, which can lead to legal action, workers’ compensation claims, and other punitive measures.
Adherence to standard lighting levels and requirements helps create a safer work environment and mitigate the risk of costly fines or legal liabilities.
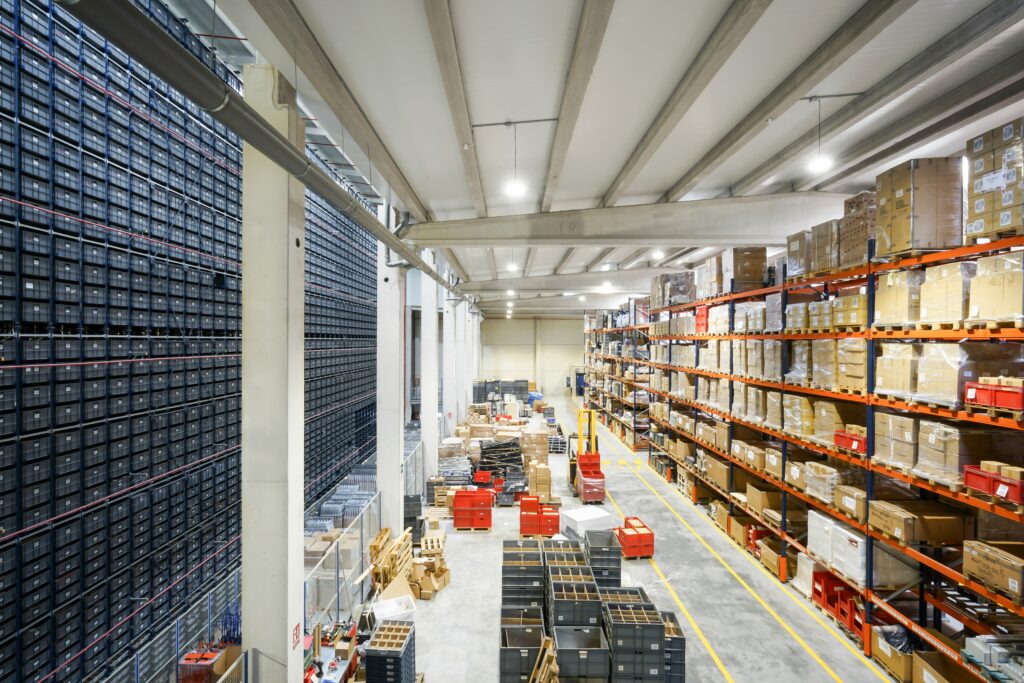
#5: Energy Efficiency and Cost Savings
Implementing an energy-efficient lighting solution, such as LED technology, is the optimal solution to ensure safety in the workplace and reduce operating costs.
With LED lighting, your warehouse is provided with high-quality illumination. With its advanced technology, LEDs produce crisp, clear light that is similar to natural daylight. This allows better visibility, comfort, and alertness while working.
LEDs emit less heat and will save you up to 80% energy compared to conventional lighting systems. Also, the use of LED lighting in warehouses will eliminate periodic tasks, such as lamp control and replacement, because of their longer lifespans.
Currently, our team runs a lighting design and an ROI analysis for our customers for free to help you achieve your warehouse lighting requirements without overspending and buying lights that are too bright and add more energy than necessary. You’ll also be more likely to get a larger rebate from your utility if you don’t over-engineer your lighting.
Conclusion
According to the US Energy Information Administration, around 44% of commercial buildings have switched to LED lighting in 2018, and long-term energy projections show that LED lights will be supplying up to 95% of commercial lighting needs by 2050.
As businesses nationwide upgrade to LED lighting, many warehouses have also begun making the switch, replacing old, outdated fluorescent, incandescent, and HID lights to energy-efficient LEDs. If you haven’t made the switch yet, allow our team to show you how an LED lighting solution can provide your facility with adequate lighting and create an improved workplace with happier employees.
Combined with LED lighting, Forthright LED Lighting has been in the field of energy for nearly 20 years. Our team can help you in assessing and implementing the best LED lighting solution for your warehouse. If you’re interested in learning more or have questions, we’re happy to help! You may book a free introductory call using this link so we can discuss your facilities’ current lighting issues, possible improvements, energy savings, and possible rebates. We look forward to hearing from you soon!